COVID-19 spurs creation of urgent projects
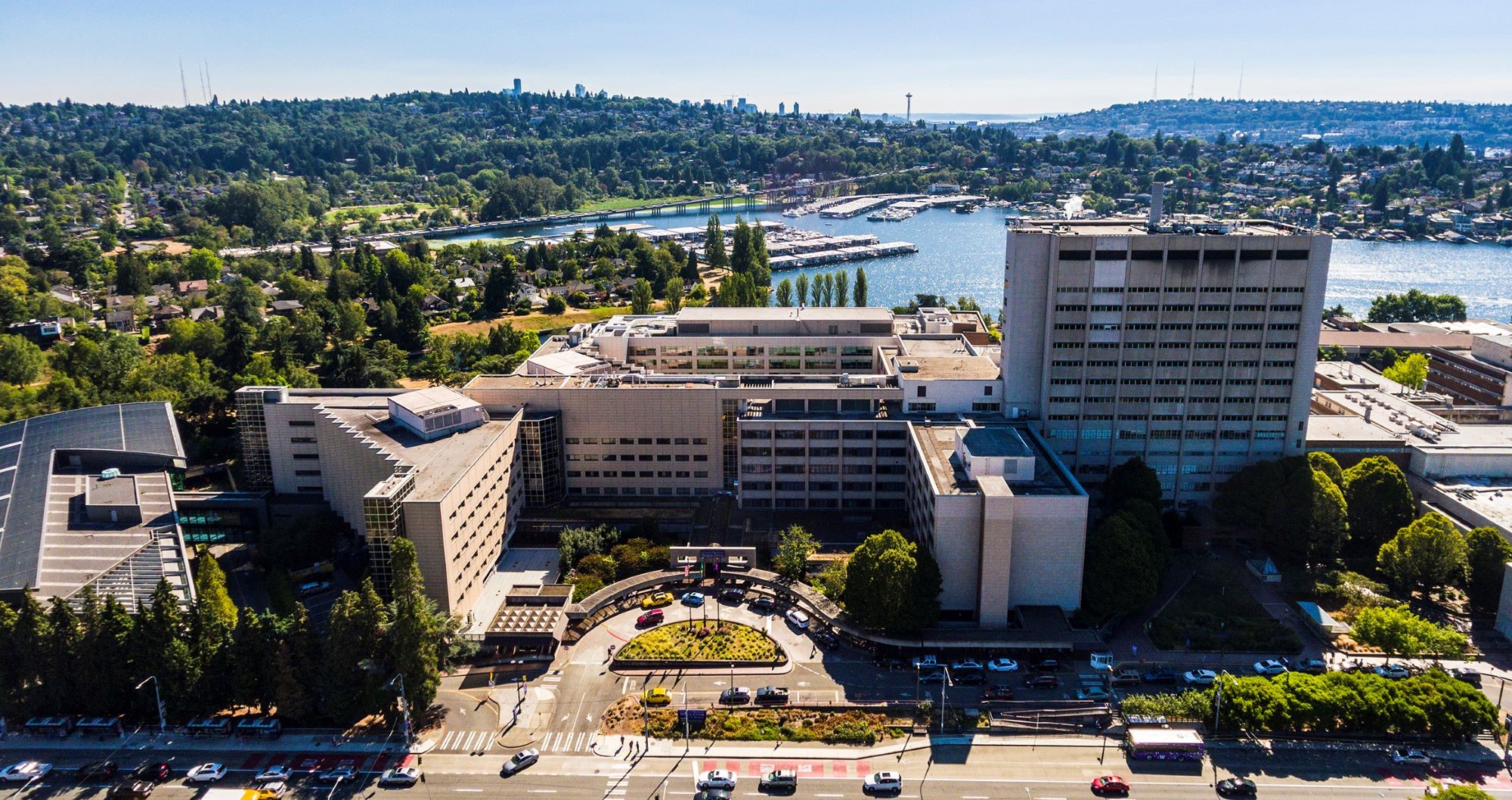
When Paul Ramsey, MD and the CEO of UW Medicine calls, people know it’s for a good reason.
"All hands on deck"
"All hands on deck"
Such was the case on March 5, when UW Facilities’ Rich Dierck received an urgent request from Ramsey to construct new space needed to increase COVID-19 testing capacity for the Brotman Baty Institute. The Institute, located on South campus near the Medical Center, was founded by UW Medicine, Fred Hutchinson Cancer Research Center and Seattle Children to study medical genetics, cancer biology, infectious disease and technology development.
So, Facilities staff partnered up with UW School of Medicine project management to build extra lab space that can be used for more testing of COVID-19.
Dierck, assistant director of construction in UWF’s Maintenance & Construction department, says the project definitely required an all hands on deck response.
“Additional equipment had been ordered specifically for this effort with a three-week lead time to arrive by the end of March, and the expectation was to have the room ready to install that equipment as soon as it arrived.”
Extra lab space created
Extra lab space created
The room has been designated as a BSL2 (Biosafety Level 2) lab and is being used to expand testing capabilities of COVID-19.
“We completed the work the same week the equipment arrived, finishing up the earthquake strapping and plugging in the equipment so that lab workers could begin using that equipment at the end of March,” adds Dierck.
On March 19, UW Facilities received another work request from Brotman Baty Institute: separate one large space into two rooms, creating a BSL2 lab and the other, a space where the researchers can work on their computers and analyze data.
The two rooms were separated with a door, and repairs were made to the rooms.
Krista Lessner, who managed these projects, says, “To me the most difficult part was the need to have the room ready by the time the equipment arrived. Nineteen shops and over 50 Facilities personnel either helped support or worked directly on these projects. There was a lot to accomplish in a few weeks, especially when most shops were already working at full capacity on other projects. I’m thankful for having so many people come together and reallocate resources to complete these projects during a time of an emerging crisis.”
Once these spaces are certified by UW Environmental Health & Safety (EH&S), they will be used to expand testing of the COVID-19 virus at the Brotman Baty Institute.
Heavy lifting required
Heavy lifting required
UW Facilities also received a work order requesting assistance with removing an older biosafety cabinet and replacing it with a new model.
Preparations to the room that houses the new biosafety cabinet required a number of changes, including modifying/ fabricating HVAC ducting & trim, providing dedicated power to the cabinet, seismic bracing and a ceiling refresh.
Christine Von Lossow, who served as project manager for this effort said the real challenge was coordinating with all of the different service teams during very restricted operations.
Additionally, Von Lossow said, the teams were thrown a definite curveball.
“We actually even had to call in the elevator mechanic as the freight elevator went down and we couldn’t get the old cabinet moved out to make way for the new one. Luckily, due to the project need and urgency, all teams came together and achieved our project goals in under two weeks,” said Von Lossow.
Other projects at least partially driven by COVID-19 are in progress, staff say.
Many Facilities employees from the following departments and shops were involved in these recent projects: plumbers, carpenters, sheet metal, electricians, painters, mechanical engineers, HVAC, the Lock Shop, fire sprinkler, fire alarm, custodians, hazardous materials, Moving Services & Surplus, flooring, and masonry.