SHIP Grant Project
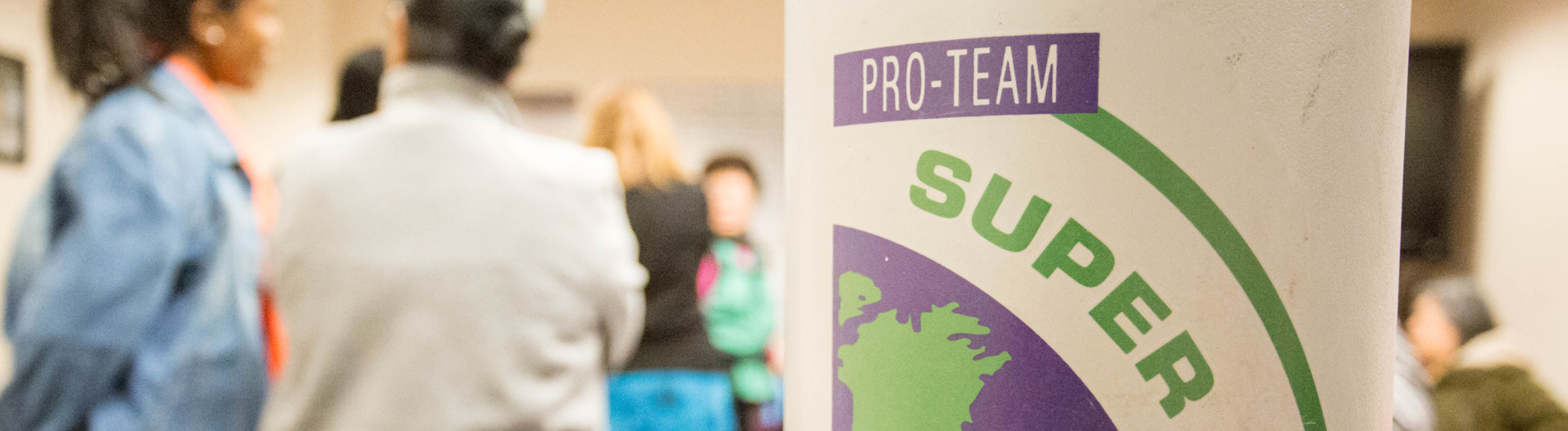
UW Environmental Health & Safety (EH&S) and Building Services Department (BSD) recently partnered up for the Safety & Health Investment Project (also known as the SHIP grant project or Participatory Ergonomics Project). Funded by State of Washington, Department of Labor & Industries (L&I), the project team engaged BSD custodians and leadership, UW EH&S leadership, Facilities Services Safety Team, and professional ergonomists in a year-long collaboration. Their collective efforts focused on the goal of developing ergonomic solutions to reduce risk of musculoskeletal injuries among custodial staff.
“Worker injuries and how we can prevent them are really important to me,” said Dr. Debra Milek, medical co-director for EH&S within the occupational medical clinic at Harborview Medical Center. “I looked at the data and saw that the third highest area for workplace injuries was in facilities and custodial work. There’s a lot of focus out there on office ergonomics, using the right chairs, desks, lumbar support, keyboards, screens, etc. However, there isn’t a lot available for custodial workers. The BSD custodial team had already worked with L&I on building a better custodial cart, but there wasn’t a programmatic or systematic way for them to make safety improvements. I spoke with Facilities Services Safety Manager, Tracey Mosier, and it seemed like BSD would be very receptive to the idea of pursuing this grant and taking on this big task,” said Milek.
Mosier was right. Gene Woodard, director of Building Services Department, quickly agreed to the collaboration when he was contacted by Dr. Milek and EH&S. "BSD leadership cares deeply about our custodial team's health and wellness—along with the outcomes of the work that they do every day. Custodial work is very physical, so we had a strong sense that this project could help us discover ways to make the work more comfortable. Our unit immediately got to work with EH&S in developing the grant proposal, objectives and what we would like to accomplish," said Woodard. The project plan was also shared and discussed with the union that represents custodial employees.
STEP BY STEP
STEP BY STEP
Collecting information about cleaning tasks involved the development of a pre-modification survey highlighting 16 common custodial tasks. “The first phase of the project was to find out what repetitive tasks were causing BSD custodians the most discomfort, as discomfort itself can be a predictor of future injury," said Milek. "To do so, we used pictures to help identify tasks within the survey format. We then administered surveys to volunteer groups of custodians and supervisors." Interpreter services were also provided for individuals in need of assistance while reviewing survey materials.
“A big concern we’ve researched is the intensity of discomfort that our custodians feel,” said Woodard. "We systematically went through each task and had a group of custodians identify which ones create the most discomfort for them," he said.
"If you don’t ask, you’re not really going to find out," said Milek. "Custodian input has been so valuable and integral to this entire process. We couldn’t have done it without them.”
During phase two, the pre-modification survey results were used as a guide in determining the five tasks that custodians cited as causing the most discomfort, which include: wearing/using vacuum backpacks; scraping floors before waxing; cleaning toilets; opening dumpster lids; and picking up trash from auditorium/lecture floors. The group then set out to develop improvements through a participatory process.
The project team formed four small groups in order to address challenges and determine possible ergonomic solutions for each of the five identified tasks during phase three. “It was a great opportunity to meet other custodians and specialists," said George Ceratto, Area D custodian. "I enjoyed learning about the research/development process and the implementation of our findings. It’s interesting to be behind-the-scenes and see what exactly goes into making ergonomic improvements.”
“BSD’s mantra became ‘We’re trying to save our backs!’,” said Woodard. With that particular concern in mind, each group ultimately developed and implemented the following potential solutions during phase four:
- Proper harness fitting and training for vacuum backpacks.
- Scraping floors with longer-handled and height adjustable poles, and/or small scrubber machines.
- Basing length of toilet brush handles on user height.
- Telescopic trash-grabbers with magnets for picking up trash from floors.
- Use of lift devices for holding dumpster lids, (a challenge that students from UW Engineering chose to take on as a class project in collaboration with the SHIP team).
There was an unexpected discovery that popped up while researching toilet cleaning: restroom toilet stalls.
“The doors didn’t originate as a problem, but we recognized them as an issue while we were processing the task of toilet cleaning," said Ceratto.
“Not only were brush handles and bending over an issue with cleaning toilets, but so was using hips to hold stall doors open, as well as bending and twisting at odd angles,” said Milek. "We tried a few solutions and ended up installing magnets on the inside of stall doors so that each door could be held open automatically. It’s a really elegant solution that saves custodians a lot of time and prevents awkward movements.” BSD maintenance custodians assisted witht the installation process.
During phases five and six, a post-modification survey was distributed and pre- and post-risk assessments were observed. “We’re committed to building on our environment of safety and finding real and sustainable solutions that help our custodians,” said Woodard. "We’re also committed to working solutions in a way that engages our custodians, so that they continue to have a say in how they do their work and improve the process."
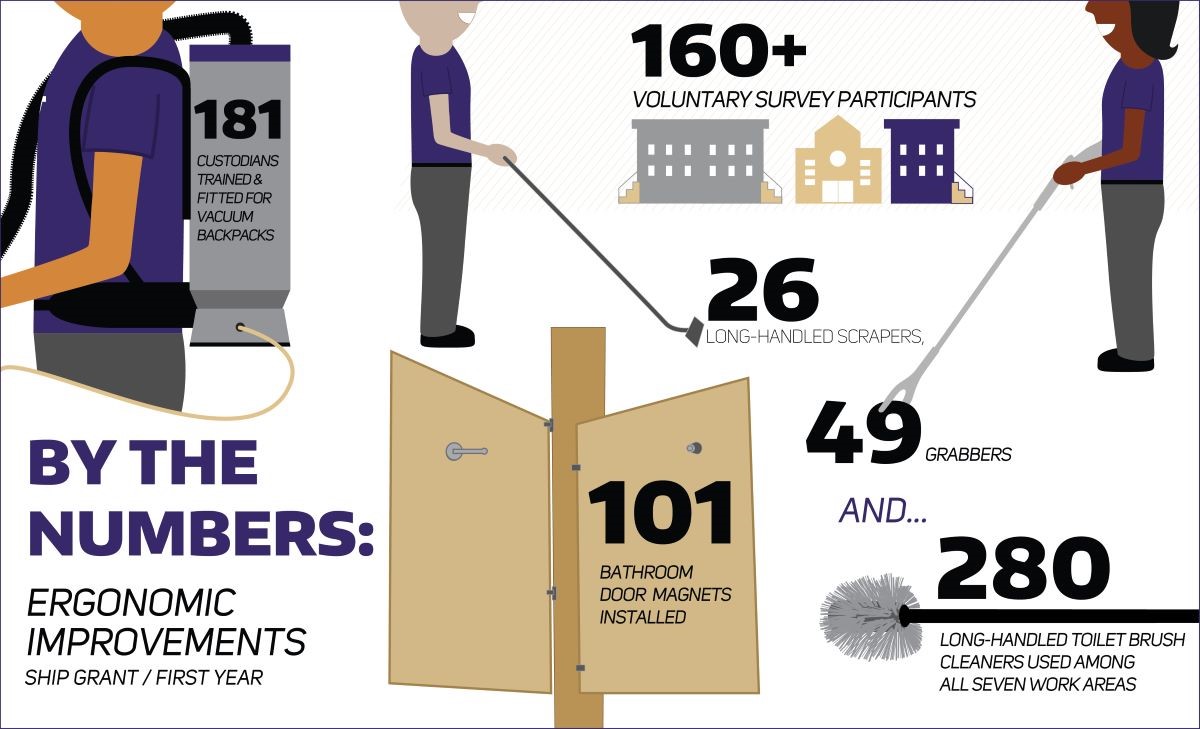
CREATING CHANGE
CREATING CHANGE
Along with making a difference in the lives of BSD team members, the SHIP grant project also holds the potential of shifting the status quo in terms of the custodial industry. “In terms of equipment, there’s not a lot of advancement out there. We’re hoping one of the outcomes of this project is that manufacturers are more receptive to feedback,” said Milek. "When Gene (Woodard) presents the project’s findings during meetings and conferences, our efforts can help influence others to take a look at the ergonomics and discomforts of their custodial and facilities work. We can become more involved in creating new and improved designs, because so many of these issues stem from having a one-size-fits-all solution. One manufacturer we’ve worked with is receptive to our feedback and is changing their designs. That pressure, we’ve found, is really necessary to making changes."
Woodard echoed this sentiment of a large-scale culture change within the field of custodial services: "Making recommendations for improvements to various cleaning tools by end users such as university custodians hasn't been systematically done before in our industry."
Additionally, the SHIP grant team's findings on strain and injuries through repetitive movements are catching the eye of the medical community. “The occupational medic physicians I’ve talked to have treated custodians in the past and continue to do so. They’re very interested in the progress we have made within the last year. It feels like we’re on the cutting edge; we’re trying something new and making improvements that will benefit many people,” said Milek.
Ceratto added: “As we’re learning through our Lean huddles, the work area managers know what we need to do each day, but it’s the custodians that are familiar with the quirks within every building and every cleaning task they're responsible for. Through this project, we’re seeing ideas that people have developed on their own but were unable to share with others. Programs like SHIP are helping to implement those ideas with a focus on safety. I certainly would recommend other custodians to get involved in this process. I think it’s a best practice to get involved and volunteer for programs. I’ve enjoyed participating; it’s been a pleasure working with the team!”
LOOKING AHEAD
LOOKING AHEAD
Since funding expired in May 2016, BSD has committed to continue the project as a department-run effort through May of 2017. Working with Dr. Milek on a quarter-time basis, the new ergonomics team—which includes representatives from all custodial work areas—meets weekly to keep the project moving forward. Jessica Lisiewski, who splits her time as ergonomics project manager and UW Recycling program coordinator, oversees the team's progress.
“The current team has the opportunity to build on the improvements that the inaugural ergonomics project team researched," said Lisiewski. "By continuing to improve the health of UW custodians now, our department has the potential to impact the entire custodial team within BSD for years to come. The ergonomic study is an important mission to make working within BSD safer and more comfortable."