Inside a Fire Box
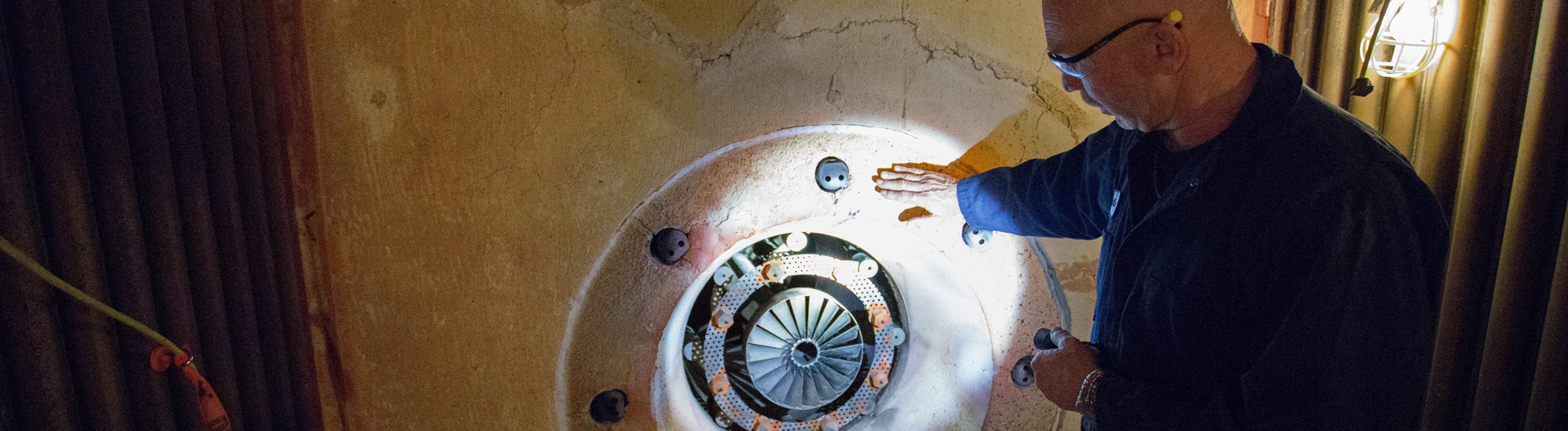
Power Plant Mechanic Acting Lead Alan Horne describes how air and natural gas combust to heat water, becoming steam that serves all of campus.
Every summer when the Northwest’s gray skies give way to a beautiful blue, shining views of Mt. Rainier and a long-awaited burst of warm weather, the Power Plant’s skilled maintenance staff take apart campus’ boilers for their yearly inspections.
These inspections not only help to ensure that equipment is operating properly and meets the highest of safety standards, but that the boilers are running efficiently, part of Facilities Services’ goal to champion environmental stewardship.
Campus buildings require heating and cooling at all times, particularly in sensitive lab spaces, basements, or glass-clad buildings. Over the summer the Power Plant doesn’t need to provide as much steam heat, so it is able to rotate through the boilers and conduct maintenance inspections on each one. In the winter the crews do the same thing with the Power Plant’s collection of chillers.
Power Plant Mechanic Acting Lead Alan Horne’s first concern with this process is ensuring he’s able to enter the boiler safely, which involves a thorough lock-out tag-out process, as well as a confined space entry process.
“If we want to tag out a boiler we assign a lock box,” said Horne, pointing to a case with dozens of padlocks. “Each case comes with a checklist, and that checklist tells you all of the valves and components of that boiler, so you go around and inspect each component, locking it out and checking it off the list.”
To safely enter a boiler, maintenance staff diligently follow confined space entry procedures, fill out entry permits, notify the Seattle Fire Department, ventilate the empty boiler space, and test the air quality and other factors and note them all down.
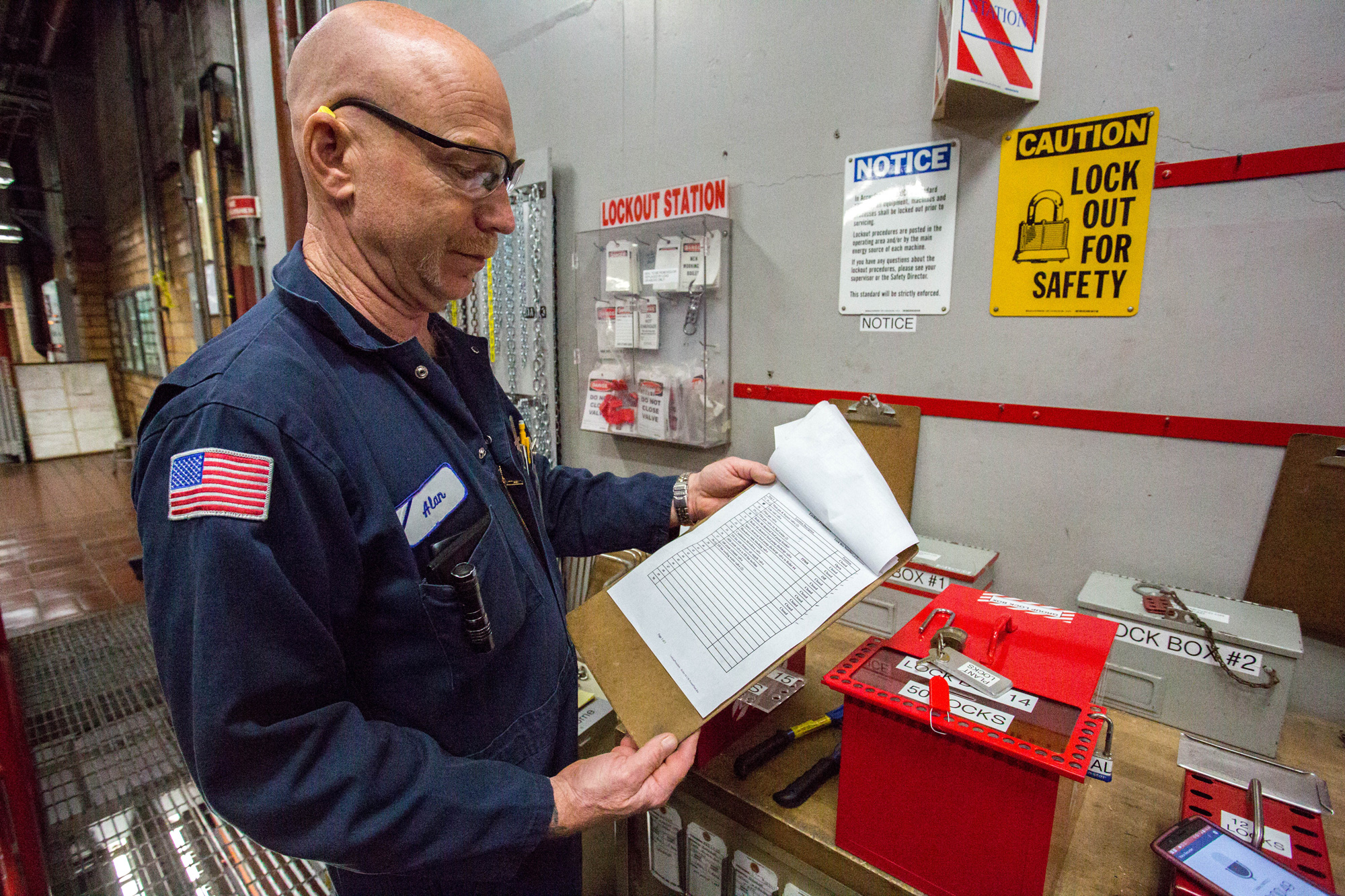
Horne showcases the team's thorough lock-out tag-out procedures prior to entering the boiler.
Boilers are designed to combust natural gas and air under intense pressures, and inspections involve crawling through small cutouts into completely enclosed spaces. With all of the risks, Horne says his team takes safety very seriously.
“All of these processes are put in place to keep us safe. When we enter the boiler we lock up the case containing the key with our own personal lock so that nobody else can access it,” said Horne.
When the team inspects the inside of the boiler, referred to as the fire box, they look for bumps and inconsistencies in the tubes that compose of the boiler’s inner walls, which carry water as it becomes steam. They also look for color changes that may indicate flame impingement or a leak in the tube.
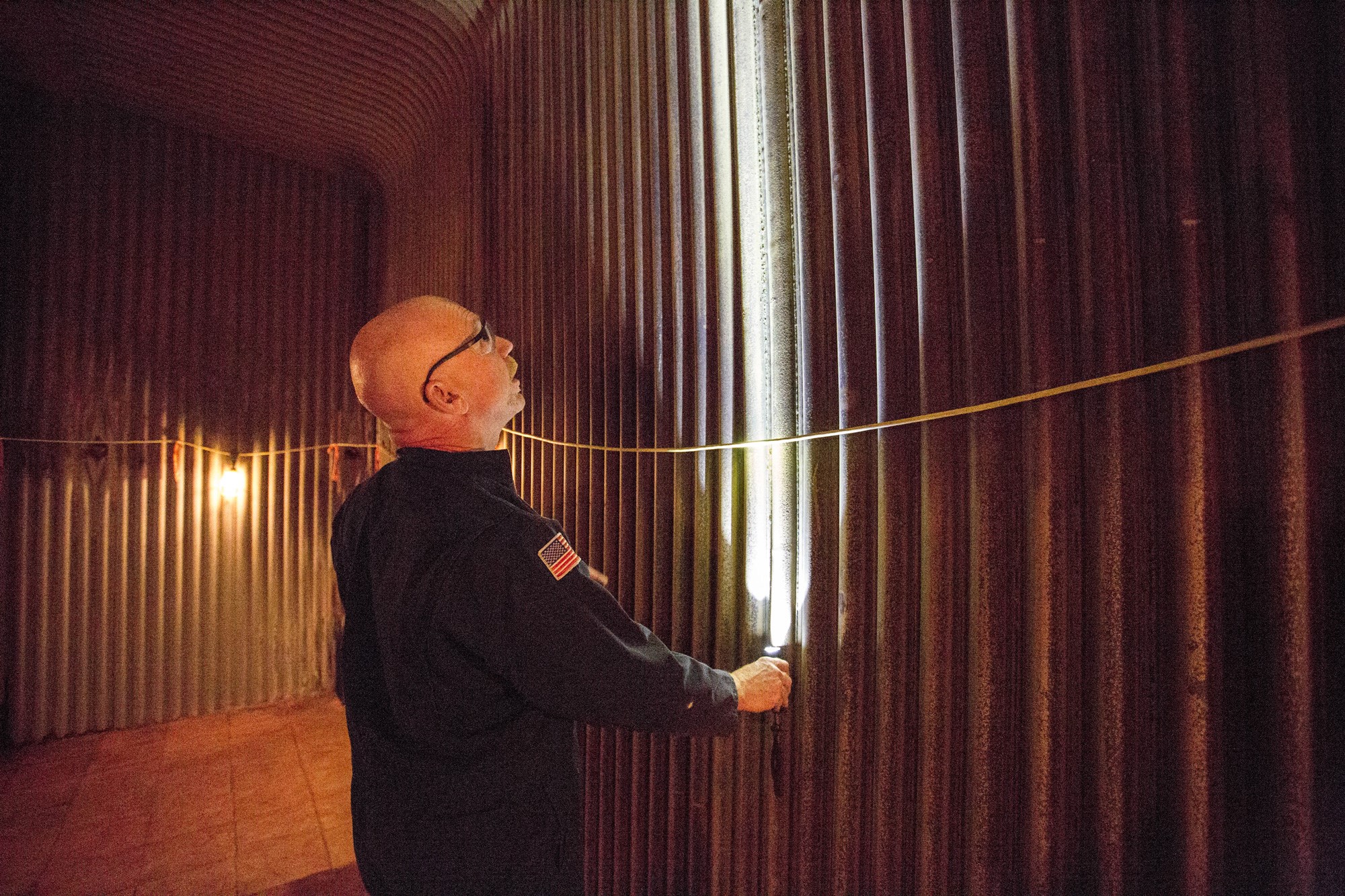
Alan Horne inspects the tube that compose of the boiler's inner walls, looking for bumps and inconsistencies.
“The water comes in from the top of the boiler and cirulated down. As it’s heated and becomes steam, the steam rises up. The tubes inside the boiler are filled with water and steam. As the steam leaves the boiler it is replaced with water. This is called ‘natural circulation,’” explained Horne.
While the team inspects the inside of the boiler, they send off safety valves and other components for thorough testing and inspection before re-installing them, just in time for cooler weather in September and October. As students return to campus and buildings require more heat, boilers are brought back online after their summer hibernation.