Powering up campus
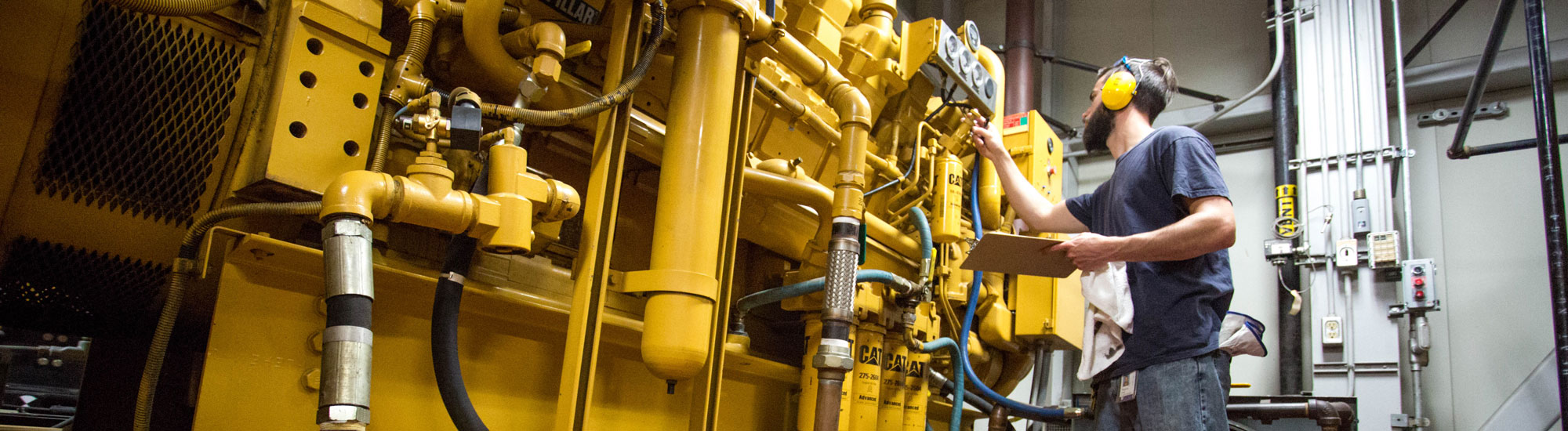
Power Plant Shift Operator Raymond Shell checks on one of the University's five diesel generators before the monthly backup tests begin.
The power plant electrician asks the group if they’re ready with their stopwatches, then counts down. Three—two—one—the lights go black for a beat. Five giant diesel engine backup generators, each larger than a pickup truck, begin to roar.
The lights are back on; surgeries continue without missing a beat, and priceless research continues to stay frozen in a lab on campus. It’s a monthly test of the University’s backup power generation capabilities down at the Power Plant.
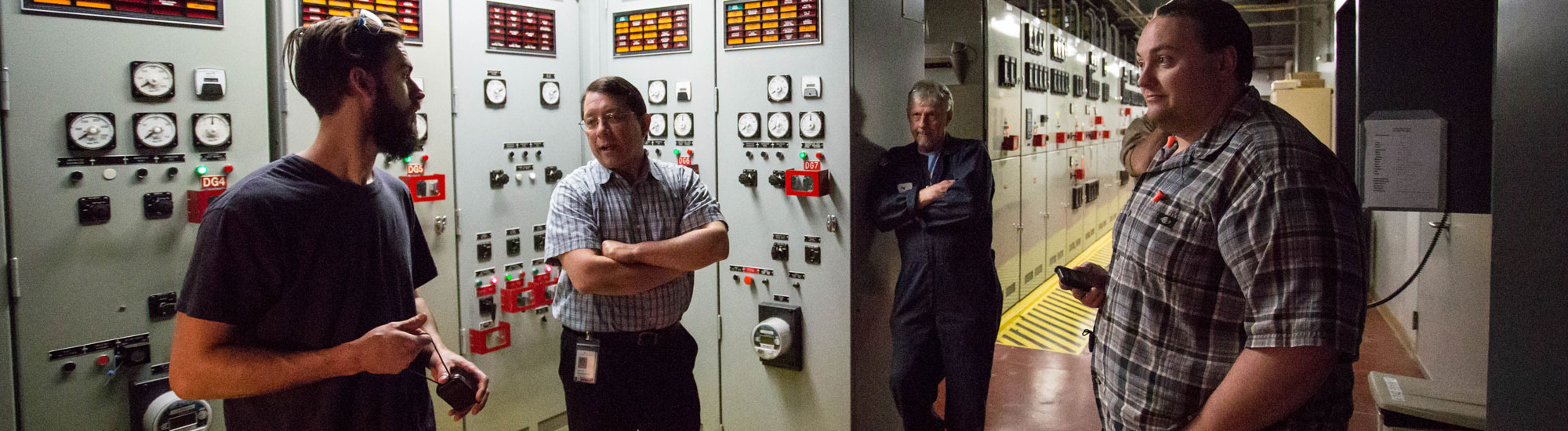
From left to right, Raymond Shell, Mark Kirschenbaum, Ray Massie and Mark Easton during the monthly test of the power plant's backup power generation capabilities. Shell and Easton hold stopwatches, timing how long it takes the system to notice the power is out and begin running.
“There are two different kinds of tests we do on a monthly basis,” said mechanic Ray Massie. “Then, once a year, we have a ‘no-kidding, let’s see what this thing can really do’ test where we open up the generators and run them at capacity for four hours to ensure they can handle maximum loads.”
The Power Plant may be a bit of a misnomer. While it’s capable of providing up to 10 megawatts of power for campus to use during emergencies, powering the medical center, mission-critical lab facilities, and emergency lighting and door systems for campus, the power plant doesn’t produce enough electricity to power the entire the University every day. In fact, the University of Washington obtains most of its daily electricity from Seattle City Light, while the Power Plant provides central heating, cooling and air for most buildings on campus, as well as backup/emergency power using diesel generators.
Read more about the Power Plant in our post about the plant’s night-shift employees, and how Facilities Services helps prepare the University for emergencies. And finally, learn more about the University’s daily electricity use on its energy dashboard.
Testing the University’s backup power capabilities isn’t just for peace-of-mind, it’s a regulatory requirement nationally from the National Fire Protection Association that came into place after Hurricane Katrina. While the NFPA has required testing for many years, it’s an extended duration test that came out of the Katrina disaster.
“After Katrina quite a few hospitals in New Orleans ran into power problems,” said Mark Kirschenbaum, assistant director of campus utilities and manager of the Power Plant. “Hospitals in that region were able to start up their backup generators, but then they quickly failed. They hadn’t tested their backup systems long enough or with a large enough load to discover any problems.”
The requirement for the four hour load test is every three years. The University runs short-duration full load tests every month, and the four hour test every January, exceeding the NFPA’s requirements.
“It’s not just about crossing Ts and dotting Is,” said Massie. “The University, the medical center—they depend on us to keep running. We need to make sure our systems really work.”
Testing the backup systems isn’t just a matter of flipping a switch or turning a key and revving a few engines.
“This isn’t just a test of whether the engines start,” said Kirschenbaum. “It’s testing the ability of the system to recognize a loss of power and then perform an automatic startup – and can handle the loads we place on it.”
Power plant staff work together with campus’ high voltage electrical shop and utility workers at the medical center to meticulously check every switch, breaker box, pump, battery, oil levels and more to ensure everything is ship-shape. These checks take place at the beginning and end of every test and an additional weekly check is conducted to ensure the system is ready to respond to an emergency.
“Our work is very thorough and highly detailed,” said Kirschenbaum. “We look at every switch position and note it down.”
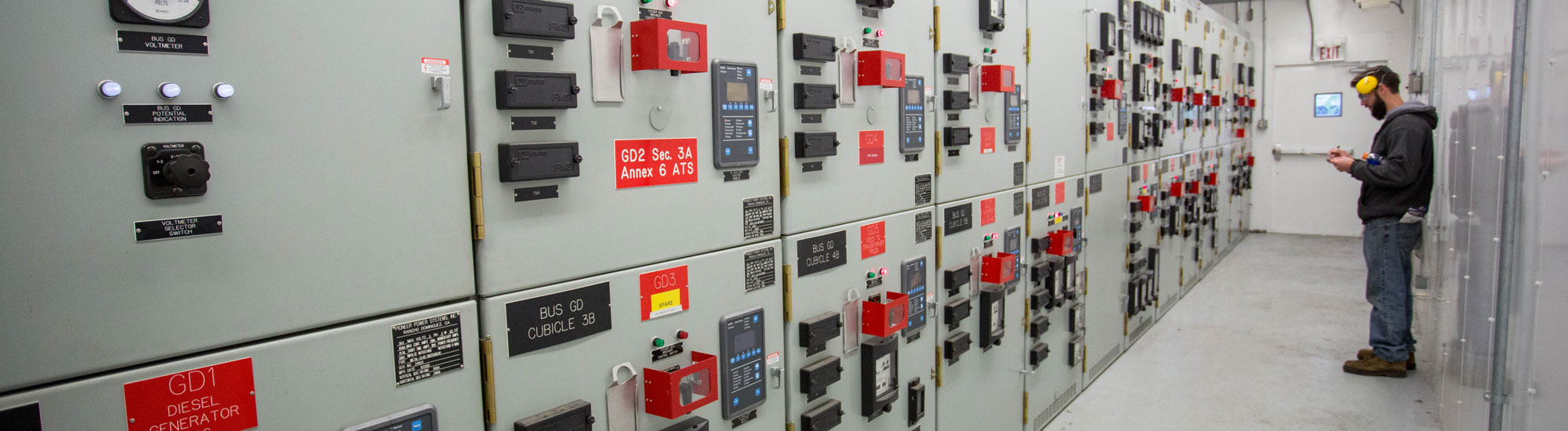
Power Plant Shift Operator Raymond Shell notes down positions of switches and levers on the University's power distribution system. These mega-sized circuit breakers are checked regularly, as well as before and after every test of the backup power system.
The tests begin with what the power plant engineers refer to as a “dead bus” test, measuring the amount of time it takes for the system to recognize it isn’t receiving power and start up generators. In the case of Wednesday morning’s test, it took just 6.7 seconds, the maximum time allowed is 10 seconds.
Next up is the load test. Power plant staff follow similar protocols to the dead bus test, but in this instance they’re testing how long the generators can run and at what load. The generators begin at just 750 kilowatts and work their way up to 2000 kilowatts per generator, or two megawatts each for different intervals of time.
While the engines are working hard, with their turbochargers’ steel casing glowing from the heat, power plant staff are monitoring valves and switches, and keeping in close contact with utility workers at the medical center and high voltage electricians.
After a few hours the generators are slowly powered down and the plant staff make the rounds on every valve and switch once more. While the monthly test takes only a few hours for a handful of employees to complete, testing the system has the potential to save lives and research next time the power goes out.
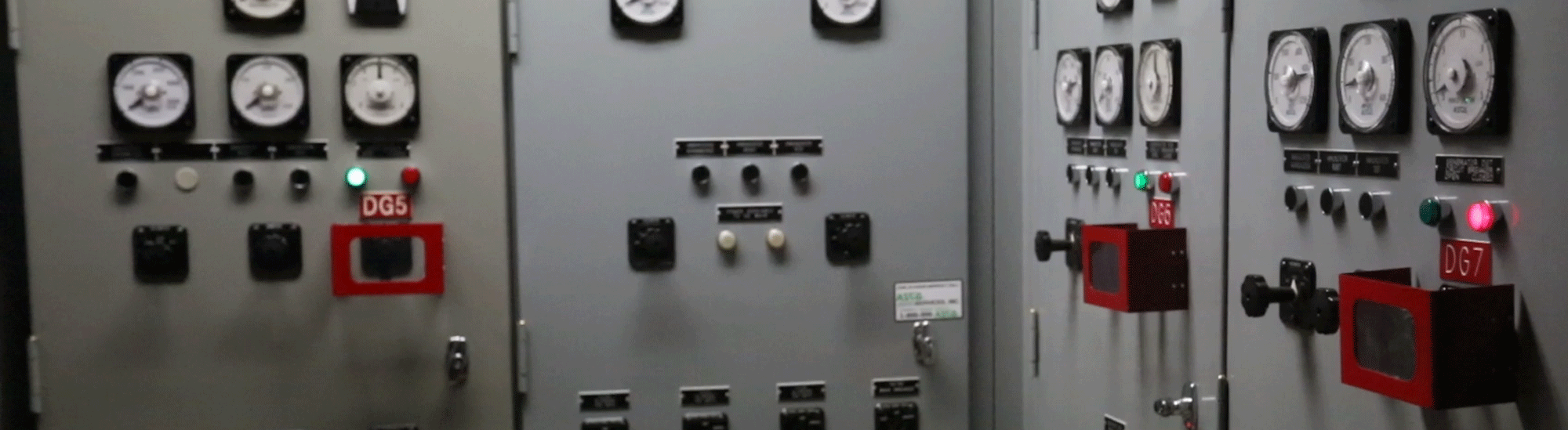
Campus Power Plant generator tests take place on the second Wednesday of every month, although you’d never know the difference unless you’re with the crew! If you’re interested in learning more about the Power Plant you can watch their in-depth video, or contact Mark Kirschenbaum to arrange a Power Plant tour.