Tweaking and tuning
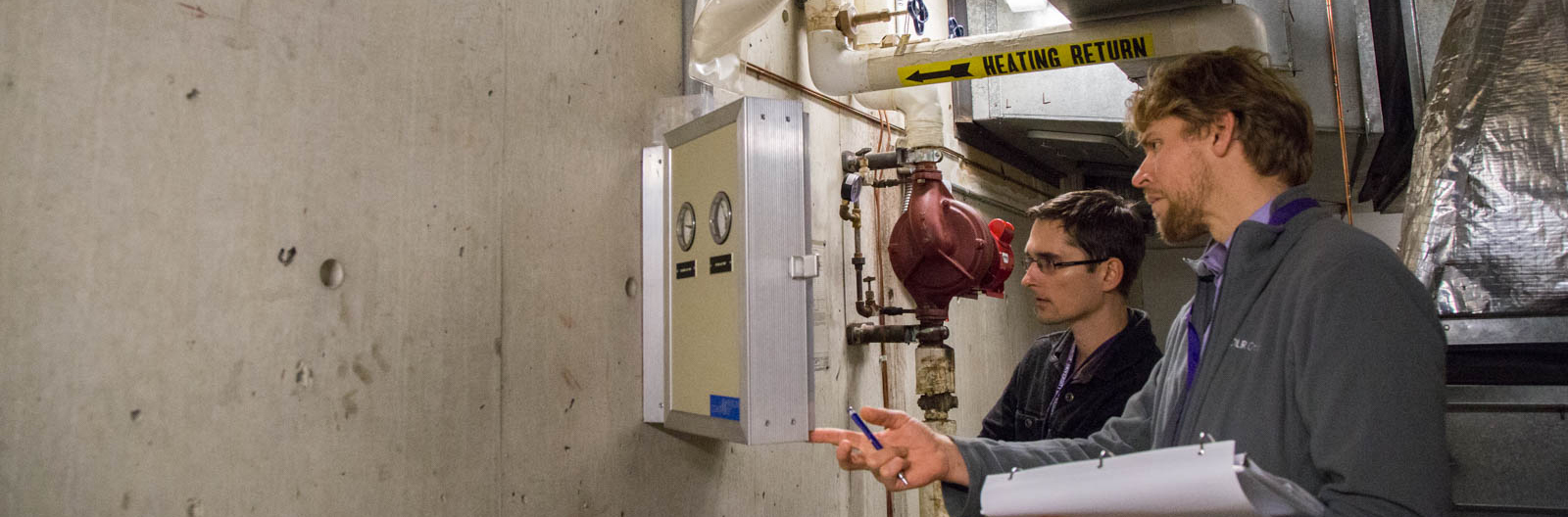
Robert Gaynor (left) and Erik Turner, energy engineers with Facilities Services, work in Condon Hall in Seattle, Wash. on Wednesday, Nov. 18, 2015 to complete an energy audit of the building’s facilities.
It’s been a long time since the University first opens its doors on our current campus in 1895.
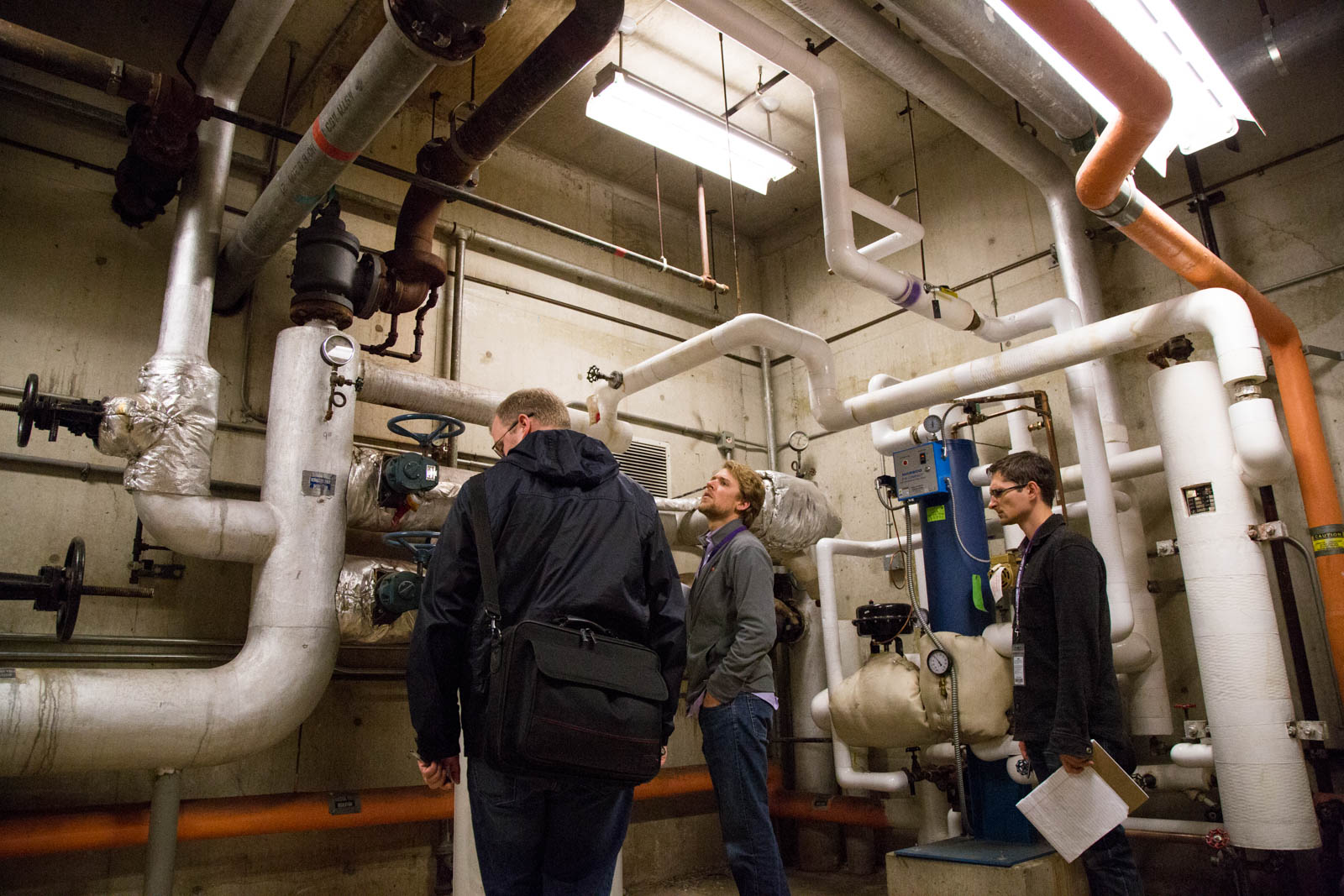
Joe Cook (left), Erik Turner, and Robert Gaynor look through the mechanical room in Condon Hall in Seattle, Wash. on Wednesday, Nov. 18, 2015 to identify the current status of the steam piping.
Now, thousands of students have flipped on light switches, plugged in to outlets, and listened to lectures in buildings maintained to last through the ages. While the buildings change over time, energy audits conducted by the Facilities Services team reveal a lot about the history of a building.
Simply put, an energy audit identifies energy savings opportunities. The audits aim to reduce energy consumption and cost in the long-term by identifying malfunctions and improvement opportunities within the building’s energy using systems. Through this process, the engineers also determine if steps need to be immediately taken for urgent matters, such as active steam leaks. Broken equipment and safety hazards, regardless of the energy consequence, are written up in a work order and sent out to the correct operating and maintenance shop.
While every building is different, facilities often share common problems, such as leaking valves, or broken actuators or sensors that are out of calibration. Most tweaks that need to be made revolve around the heating and ventilation systems.
“[Energy audits] highlight a lot that wouldn’t ordinarily be noticed by tenants,” said Erik Turner, an energy engineer for Facilities Services.
Buildings around campus were audited in the mid-1990s by Maintenance and Alterations, which is now known as FMC. The audits focused on lighting and plumbing fixtures around campus, and focused primarily low-level conservation projects. Now, each building requires a five week carried out by two full time engineers. The methodically planned sweep focuses on the HVAC equipment and primary steam, electricity, and chilled water utility systems. The audit is focused on finding cost effective and impactful waste with highest value based return on investment.
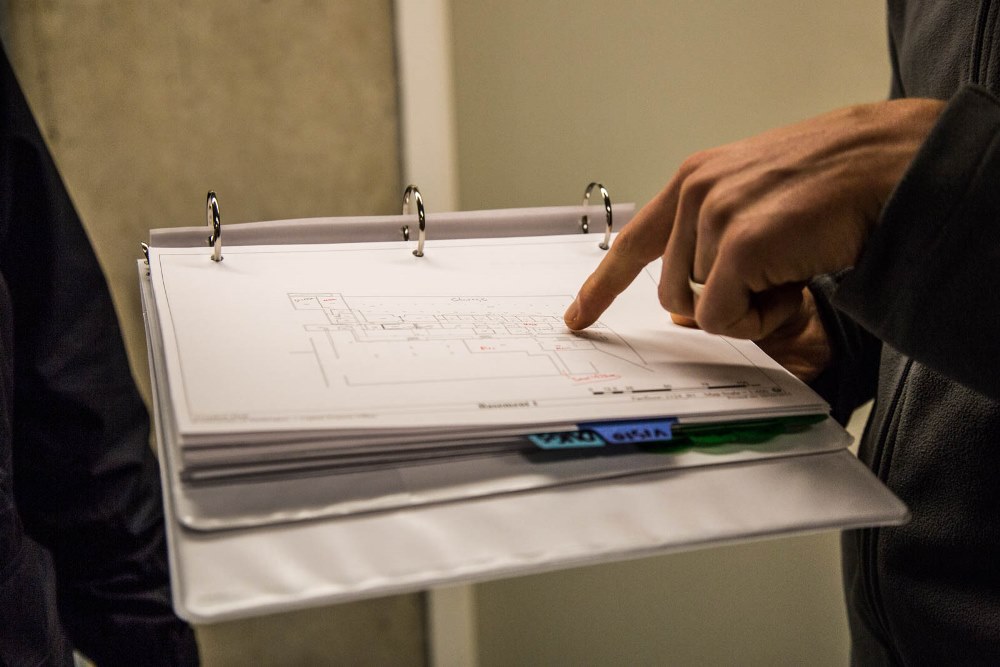
Erik Turner, an energy engineer with Facilities Services, flips through his binder in Condon Hall in Seattle, Wash., on Wednesday, Nov. 18, 2015. The binder is filled with floor plans, schematic of all the mechanical systems, drawings, diagrams, and pages to take notes during the energy audit.
When Norm Menter, the energy conservation manager, joined Facilities Services around four years ago, he took on the building audit process. Energy consumption became a top priority.
Turner and Robert Gaynor, both energy engineers for Facilities Services, were hired to analyze the buildings from head to toe.
Since July 2013, the energy engineers have been working to audit over 11 million gross square feet of campus. The energy engineers have audited 101 buildings as of December 2015, and should complete the remaining 14 buildings by March 2016.
By the end of 2015, the Facilities Services identified 391 conservation opportunities through the audits. If all conservation opportunities were executed, greenhouse gas emissions would be reduced by nearly 29,000 MGCo2e, or nearly 30% of the Seattle campus’ greenhouse gas emissions.
Across campus, conservation projects completed by the end of 2015 saved 507 metric tons of carbon dioxide equivalent.
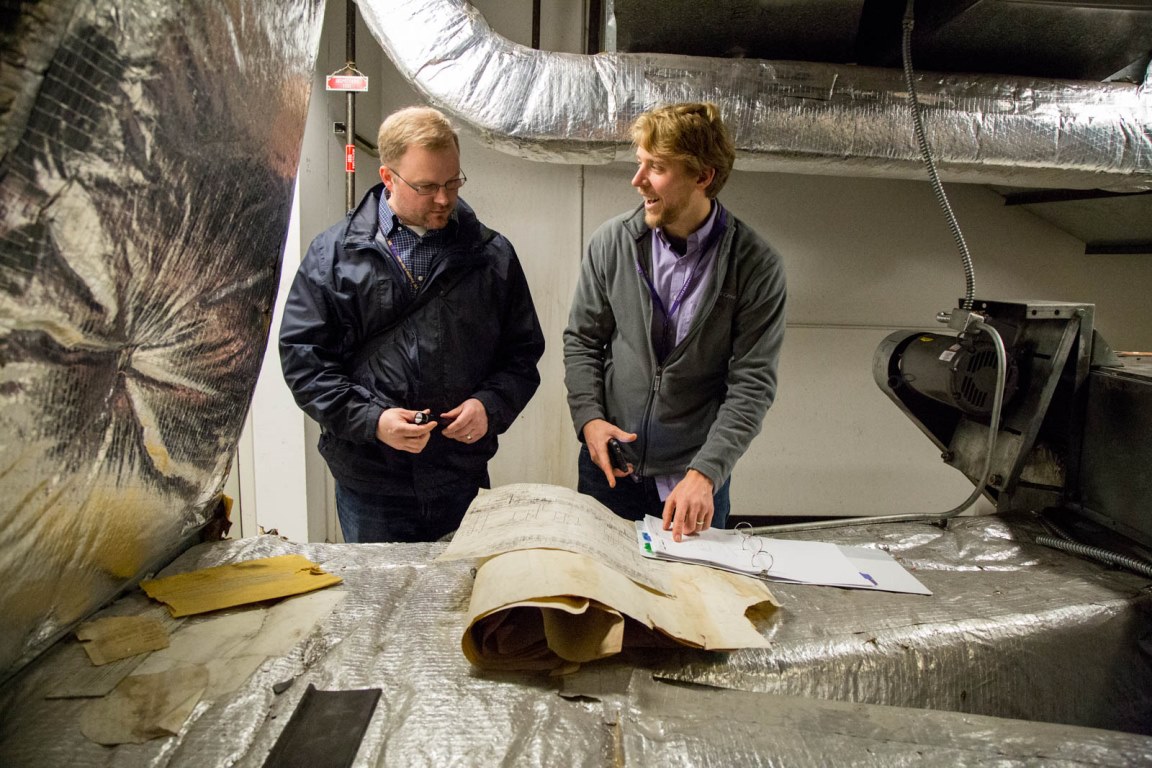
Joe Cook (left) and Erik Turner look at control drawings in Condon Hall on Wednesday, Nov. 18, 2015 in Seattle, Wash. The control drawings describe the air handling systems, and what sensors are being controlled within the building.
The HVAC (heating, ventilating, and air conditioning) systems run to keep the building comfortable, but each system can have its own glitches. Some of the HVAC systems operate through computerized software, meaning that if the physical components of the system fail, the system doesn’t operate properly. Some buildings on campus still use pneumatic controllers, which use pressurized air to control the systems components. These systems could be updated to Direct Digital Control (DDC), a modern computerized control system. The energy engineers work closely with the HVAC technicians to regularly identify problems within the systems.
Energy audits are focused on big-picture items. While many people are familiar with replacing fixtures in their own homes, such as installing new energy-efficient light bulbs, the audit process focuses on the most impactful, cost effective opportunities. Roofs, walls, doors, windows, insulation, and lights are part of the energy equation, but it isn’t necessarily cost effective to replace everything in each building.
In some of the older buildings old legacy heating systems are still used to operate the facility. The systems use a lot of air and need constant ventilation, especially if the building includes a lab environment. In some situations, the HVAC systems need to be entirely replaced, or a heat recovery system needs to be implemented. If the building wastes a lot of energy, the building may require closure, tenant relocation, and an extended period of construction time that would have a significant cost. The project could therefore have a negative energy return on the investment. In these circumstances, conservation opportunities are reported to UW planning groups to understand the cost and benefits of major project opportunities throughout campus.
After the team first steps foot in the building, they usually meet with the building coordinator for half an hour. The energy engineers prepare with a binder full of maps and empty sheets to fill out about the building. With the coordinator, the team goes over floor plans of the building and identifies major energy usages of the spaces. The team identifies when the building is normally operating, and discusses major comfort issues with the air conditioning or heating.
When Gaynor and Turner walked up the concrete steps and into Condon Hall, they were joined by Joe Cook, a mechanical engineer from Campus Engineering and Operations.
The group briefly chatted about the systems within the building, and then headed through corridors, tunnels, and in and out of the building to check for equipment.
Energy audits involve plenty of rides up and down the elevator, scouring the walls for light switches, jiggling keys to unlock the right doors, and climbing down skinny ladders.
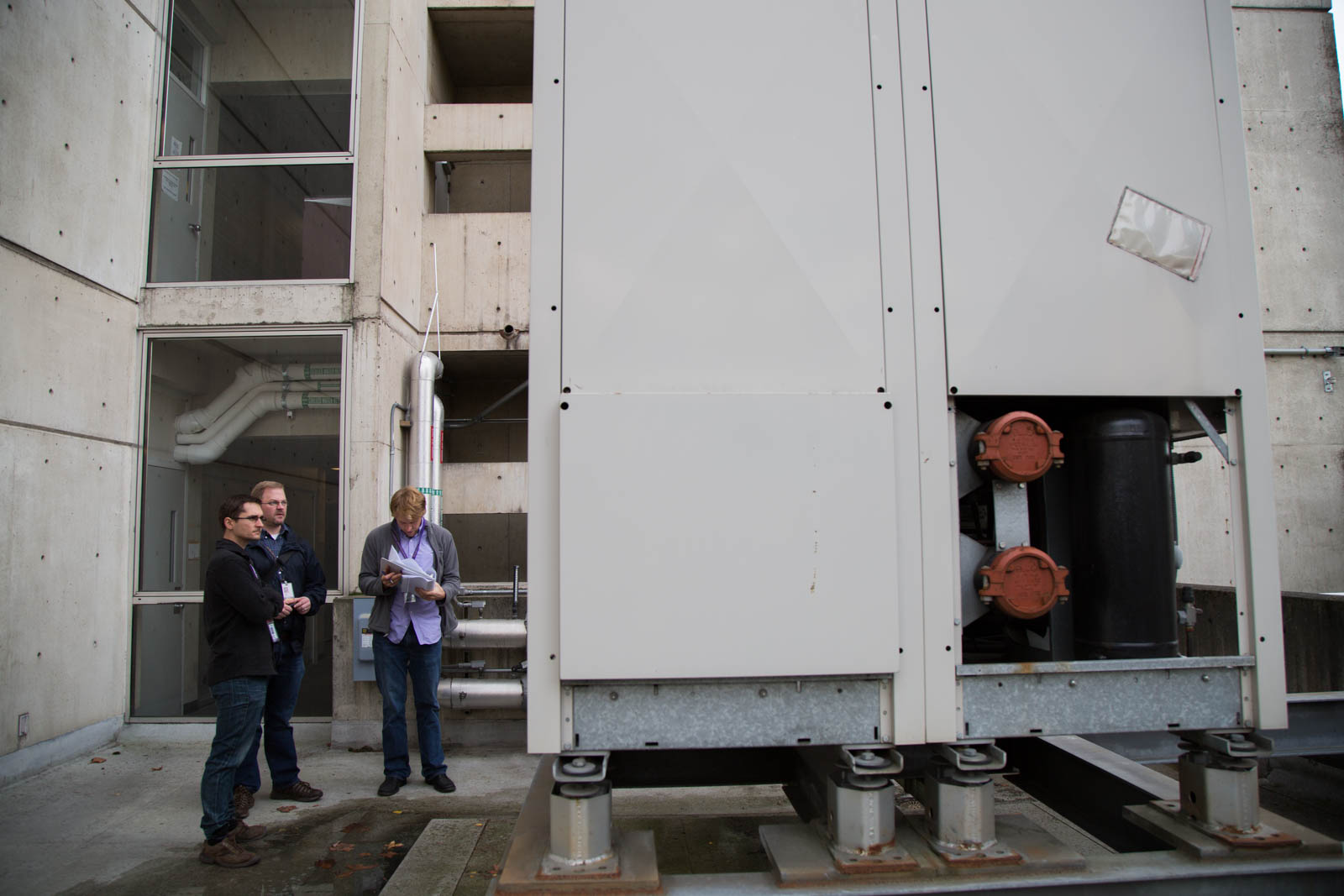
Robert Gaynor (left), Joe Cook, and Erik Turner stand on top of a portion of Condon Hall’s roof in Seattle, Wash. on Wednesday, Nov. 18, 2015 to identify pieces of equipment.
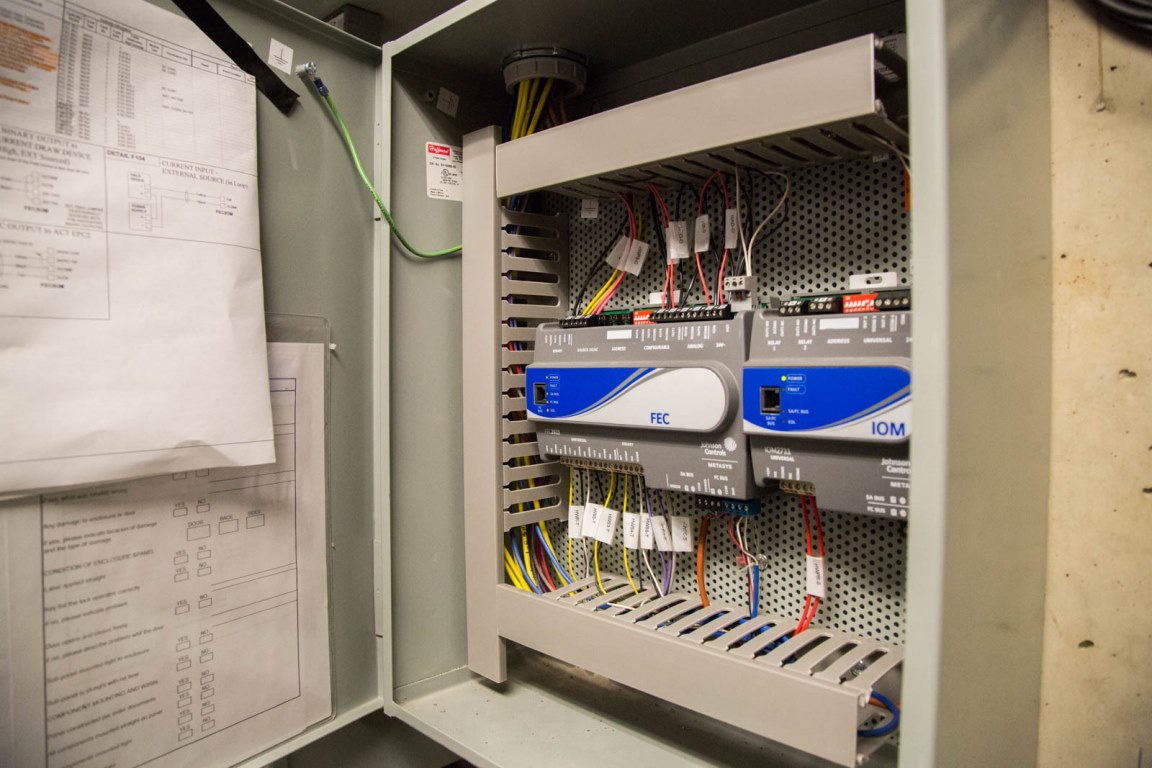
In Condon Hall in Seattle, Wash., the system field equipment controllers are used to collect metrics on the energy efficiency of the building.
For each building, the entire energy audit process takes approximately five weeks.
Buildings, just like the campus, are constantly changing. In order to accurately represent the amount of energy being used in a building, the team identifies key energy usages, and areas for improvement. The audit lets the team to take a step back and learn about existing conditions of the building before diving into the project. Age, wear and tear, and the condition of the facility all play into determining what final changes can be implemented to maintain the longevity of the building.
The projects couldn’t be completed without the help of the rest of the Facilities Services team: HVAC technicians from Shop 69, with Campus Engineering and Operations; insulation experts from Shop 17, with Facilities Maintenance & Construction; and night shift FMC electricians from Shop 41.
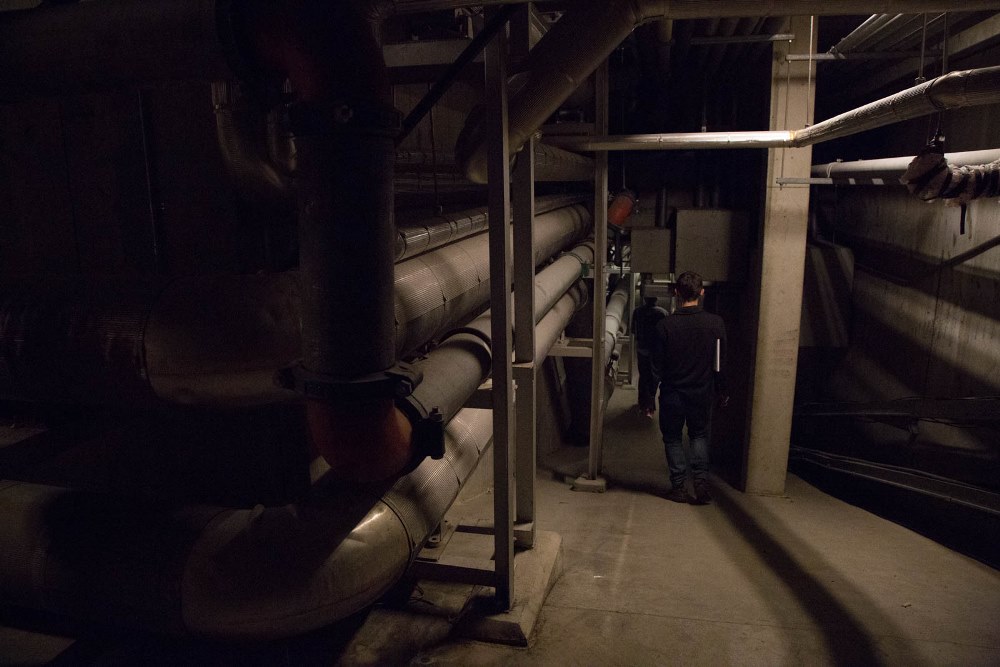
Robert Gaynor walks down Condon Hall’s utility tunnel on Wednesday, Nov. 18, 2015 in Seattle, Wash. Gaynor was looking for the BTU meter that monitors thermal energy measurements in the building’s water systems.
Facilities Services audits nearly all of campus. By the end of 2015, energy audits were completed for 93% of all state-owned, Facilities-maintained permanent facilities on the Seattle campus.
After the planning phase, the team dives into tracking existing energy use, implementing instrumentation on the buildings to monitor operations, and analyzing the collected data. After the data is compiled, engineers recommend energy-saving projects to implement. Campus Engineering and Operations, the control shops, and Environmental Health and Safety provide feedback on the implementation of the buildings’ projects.
In some cases, buildings have multiple issues. For example, Campus Engineering and the shops alerted Gaynor about a leaking steam coil in Gowen Hall.
“Since we already had an audit, we found some additional projects that would make sense to repair at the same time as a coil,” Gaynor said. But projects need resources, so many items are siphoned into higher and lower priority categories.

Robert Gaynor, an energy engineer with Facilities Services, stands on a ladder in Condon Hall in Seattle, Wash. to check out equipment on Wednesday, Nov. 18, 2015.
Some campus buildings need more work than others, but by the end of the audits, the energy engineers have a better idea of how to keep campus more sustainable.
Improving of the HVAC system in the Physics Astronomy Building basement is one example of producing sustainable results from an audit. The basement – nearly 56,000 square feet of the entire building – holds science laboratories, lab support spaces, and offices.
The system improvement project reduced building consumption by installing a variety of equipment: variable air volume terminal boxes, high efficiency motors, exhaust fan units, air handling units, and variable frequency drives. The ventilation system was also rebalanced and retro-commissioned to improve the effectiveness of the system.
After the system improvement, 489 metric tons of carbon dioxide equivalent (CO2e) were avoided, which is equivalent to 103 cars using over 55,000 gallons of gasoline per year.
It’s a small step toward a larger sustainable goal. It all starts with an audit.